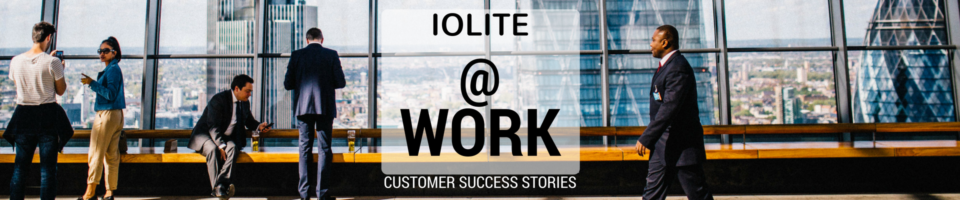
Railroad Company
Industry: Transportation
Headquarters: Kansas City, MO
Employees: 5,001 – 10,000
CRM: Salesforce.com
IOLITE Solution(s): Checklist
Challenge
Each rail yard maintains hazardous materials that need to be inspected, monitored, and maintained according to regulatory standards set by the Environmental Protection Agency (EPA). They must provide the EPA with quarterly inspection reports to certify all facilities are operating within tolerance levels established by the EPA. At any point of failure a rail yard repair team needs to be tasked and dispatched and the repair recorded.
Solution
Using IOLITE Checklist, this company built inspection checklists specific to each rail yard. Personnel can use iPads to walk through the yards and confirm the condition of the various inspection targets. If a target fails the inspection, the mobile device records the GPS coordinates of the problem, issues a repair task, and enables the inspector to record a picture of the problem with the inspection results.
Outcome
The company has a defined and repeatable process for inspecting and reporting upon facilities. Reports are regularly provided to the EPA for compliance purposes and inspection issues are routed within the company CRM so that repairs are scheduled and tracked.
Background
This company operates rail yards in major cities in the Midwest and Southern U.S. and throughout Central and Eastern Mexico.